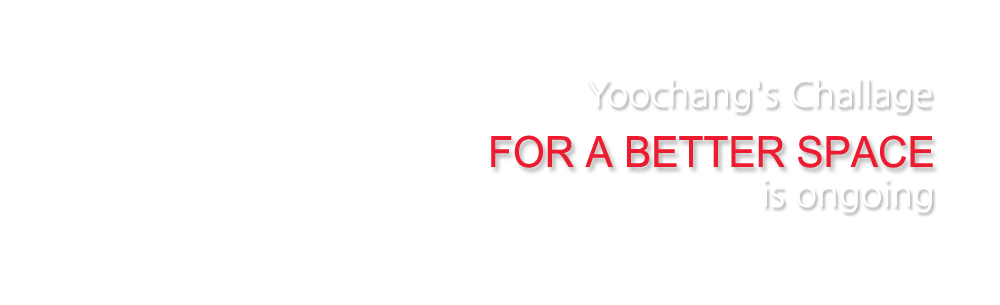
OMEGA T-BAR 25mm, 35mm

- >
- Products
- >
- OMEGA T-BAR 25mm, 35mm
OMEGA T-BAR 25mm, 35mm 
OMEGA T-BAR system has groove in its bar and by putting upper runner of wall partition into such groove such partition cab be fixed.
Thus it is aesthetically beautiful and practical and as ceiling system its work is very simple and quick. At whole sector of its installation it can play role of checking hole and also repair and checking of wiring or pipe laying are simple. There are grooves at its bar accordingly design for highlighting such grooves is possible and it is suitable to all parts of inside of building structure such as general office and shopping malls etc.
- Product outline
- Product drawing
- Information for construction
- Miscellaneous
General description for AL Ω T-BAR
(1) Definition of terms
- ① System: AL Ω T-BAR SYSTEM
- ② Method; Lay-in (A type whereby ceiling finishing panel is placed on ceiling frame)
(2) Transportation and handling
- ① Transportation: Transport after recording type, name, dimension and manufacturing date etc. on the label and then packing.
- ② Handling: Handle it according to instruction of manufacturer and requirement of the user.
AL Ω T-Bar product
(1) Material
- ① Color : white (standard color) and order color
(2) Dimension
- ① AL Ω MAIN T-BAR (25 mm x 38mm x 1.2T (for general purpose L=3600)
- ② AL Ω CROSS T-BAR 25 mm x 38mm x 1.2T (for general purpose L=600)
- ③ HANGER BOLT : ψ9mm
- ④ HANGER & PIN : 105mm X 20mm X 2.0T
- ⑤ CARRYING CHANNEL : 38mm X 12 mm X 1.2T
- ⑥ C/C JOINT : 100mm X 35mm X 10 mm X1.2T
- ⑦ C/T CLIP (for AL Ω T-bar)
- ⑧ MINOR CHANNEL : 19mm X 10mm X 1.2T
- ⑨ M/C CLIP : 38mm X 14mm X 1.2T
- ⑩ HANGER NUT : ψ9mm
- ⑪ MOLDING (for AL Ω T-bar)
- ⑫ ANGLE MOLDING : 22mm X 32mm X 0.5T
- ⑬ DOUBLE MOLDING : 15mm X 10mm X 15mm X 24mm X 0.5T
Special feature for AL Ω T-bar
- * Working is fast and simple.
- * Any ceiling plate can play role for checking hole.
- * Width of bar is narrow so it is beautiful.
- * Removes sense of monotony by presenting cross stripes ceiling.
- * By mounting upper part runner to groove it is practical.
(1) Setting centerline of building: After accurate measurement of ceiling surface set up centerline after checking other work schedule such as lightline and position of diffuser etc.
(2) Strong anchor work
- ① At the time of strong anchor work when centerline is set up mark part for fixing strong anchor (Ф9mm) at slab surface and punch hole with drill and fix it.
- ② At the time of work for cash iron insert (Ф9 mm) install it at form according to drawing.
- ③ Caution: Pay attention to intervals between anchor and insert and right angle.
- ④ It is ideal to make interval for installation as @900∼ 1,200 mm for strong anchor or insert in consideration of direction of installation of carrying channel.
(3) Molding line level check
- ① Use of water level or level
- ? ?a. Confirming position by means of drawing (confirming height of ceiling)
- ? ?b. Confirming the position by water level and ink pot string marking between positions.
- ② Caution: At the time of using water check make sure to check level after checking any presence of air bubble in hose and breaking of hose.
(4) Attachment of wall molding (using after painting angle or sea gull molding)
- ① Attach molding along the India ink line and fix wall molding by using 1" concrete nail. (interval 500∼ 1,000 mm)
- ② Be careful not to slacken the height and interval between moldings.
- ③ In connection with facilities such as curtain box it shall be attached according to specification.
(5) Installation of hanger bolt
- ① Upper part of hanger bolt is fixed to strong anchor or insert and power part of bolt is fixed with hanger and nut in consideration of ceiling height at finishing.
- ② At the place where installation duct or other obstacles are present work shall be carried out after reinforcing it according to specification.
(6) Installation of lightline
- Install lightline according to specification but it is required to have consultation with persons in charge of electricity and facility.
(7) Installation of carrying channel
- After linking hanger set and carrying channel fix it and install it with an interval of @900∼1,200 mm. The joint part of carrying channel shall be connected by using carrying joint.
- At the time of installing carrying channel make sure to install it not to be off from wall or curtain box surface more than 30 cm.
(8) Installation of minor channel
- When area for works is broad reinforce and fix with supplementary channel (minor channel) installed above the carrying channel and install it with an interval of @2,000∼3,000 mm.
(9) Installation of Main and Cross AL Ω T-bar
- ① Install Main AL Ω T-bar sturdily by using C/T cup toward right angle direction to carrying channel according to dimension of the product and lightline.
- ② Intervals for installation: for general T-bar interval is @610 mm and for Zierbart interval for installation is @600 mm.
- ③ It is installed by inserting CROSS Ω T-Bar Tip to hole of Main AL Ω T-bar.(Interval of hole: for general use it is @152.4 mm and for Ziebart it is @150 mm.)
- ④ At the time of installation of CROSS AL Ω T-Bar hole of MAIN AL Ω T-BAR shall match to hole of another MAIN AL Ω T-BAR.
(10) Installation of finishing plate (sound absorption tex/ Ziebart)
- ① Accurately set level of installed ceiling frame by bolt and nut through using water level or level.
- ② Place sound absorption tex or Ziebart on Main and Cross AL Ω T-bar after its installation. (In case of sound absorption tex fix finishing plate with hold down clip.)
- ③ Prohibit use of finishing plate with scratch, broken corner or dirtied.
(11) Installation of curtain box
- ① Manufacturing and installing products suitable to use according to specification (separate painting)
- ② Welding work is carried out concurrently therefore install work bench to enable safety in work and working in comfortable stance.